Cost Comparison Charts
Tube-Mac® Flange Systems vs. Welded Systems
Tube-Mac® non-welded piping systems take less time to install and oil flush than conventional welded piping systems that have been acid pickled and oil flushed thus resulting in an overall cost savings of 35-45%.
General Labour
No special skilled labour required to flare the pipe vs. qualified welder.
Time Savings
Actual flaring time is measured in seconds vs. hours for a welded joint.
No Permits
No special hot work permits or fire watch personnel required.
No Leaks
Tube-Mac® non-welded connections are stress free and leak free vs. added stresses from welding especially with misaligned fittings.
Stress fatigue in welds results in leaks.
Low Maintenance
Tube-Mac® non-welded flanged joints make it easy to add or change components vs. torch cutting and re-welding to add or modify a welded system.
Better Fittings
Field-bent pipe at 90 and 45 degrees reduces component cost. Field bending creates less pressure drop, which equals horsepower savings.
No X-Ray
Costly and time-consuming X-Rays are needed for high-pressure welds, but not for the Tube-Mac® non-welded piping system
Oil Flush ONLY
No acid flush chemicals and neutralizers are required, meaning no added cost or environmental issues related to chemical waste disposal. The system fluid is used in the flushing procedure and remains in the pipe for system operation, and is polished to the desired ISO cleanliness level. This also guarantees system cleanliness, which can’t be assured in a welded system. The flushing time is measured in hours vs. days to acid pickle and flush a welded system.
The following is a cost comparison summary of a typical hydraulic piping project.
Location: United States of America
Pipe Range: 1/2” through 6”
Tube-Mac® Piping System | Welded Piping System | |
Materials | $75,793.07 | $60,350.52 |
Labour | $195,096.77 | $220,612.90 |
Flushing | $83,612.90 | $225,754.83 |
TOTAL | $354,502.74 | $506,718.25 |
- Overall cost savings, installed and flushed, using a Tube-Mac® non-welded piping system, equals approx. $152,215.51 USD or 43%.
- The Tube-Mac® non-welded piping system is also faster to install and flush, resulting in savings of approx 1,521 man hours.
- While not included in this example, contractors can also save time and money with reduced commissioning and start-up times.
- The Tube-Mac® system is guaranteed to be installed clean; the welded piping system can’t provide any cleanliness guarantees.
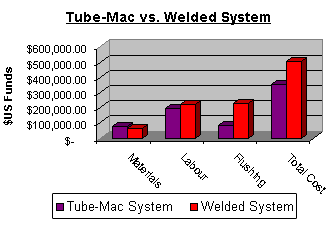
While material costs for the Tube-Mac® non-welded piping system are higher than a comparable welded system, labour and flushing cost savings more than compensate for the initial expense.
General Notes:
- This price comparison is based our knowledge and experience with Tube-Mac® non-welded piping systems.
- We have compiled information provided to us from general contractors to prepare this comparison. Tube-Mac® is not responsible for the accuracy of the information as provided.
- This price comparison is based on a typical installation with pressure and return lines varying in size from 1/2” schedule 80 through 6” XXS pipe.
- All pipe and material take-offs were done on an equal basis for both systems.
- The Tube-Mac® non-welded piping system utilized field bent pipe versus welded elbow fittings.
- All cost figures were adjusted to reflect a contractor’s purchasing practices.
- All labour rates were the same for both systems – the cost difference relates to the man-hours required to install each system.
- The labour times used are based on industry standards. Welding man-hours were based on the standard GTAW (TIG) welding for the root and one pass.
- Flushing a Tube-Mac® non-welded system requires no chemicals only the system oil. A welded system requires extensive cleaning with chemicals, followed by neutralizing and disposal of chemical waste.
- Chemical cleaning companies refuse to offer a fixed price, as they have no idea of the amount of welding contamination inside the pipe they have to clean until they begin the process. An estimate was furnished to us for the purposes of this comparison with the note that the actual cost could very well be higher.
- The installation tools and flushing equipment rentals were NOT factored into the cost of either system.
Pyplok® Weldless Swage Systems vs. Welded Systems
Based on the installation of 394 swaged fittings (various PYPLOK® sizes and material) on the USS Harry W. Hill (DD-986); pre-installation estimate.
Cost Comparison Swaging 394 Pyplok® Fittings
Conventional Welded Method | New Pyplok® Method | |
Material Costs | $3,096 | $11,657 |
Installation Labour | $23,832 | $2,992 |
Inspection Labour (x-ray vs. Pyplok® Gauge) |
$15,880 | $1,056 |
Total Labour and Material | $42,808 | $15,705 |
Actual Installation Cost (In US Dollars)
Man Hours | Labour Cost | Material Cost | Total Cost | |
Welded | 992.8 | $39,712 | $3,096 | $42,808 |
Pyplok® | 101.2 | $2,992 | $11,657 | $15,705 |
Difference | (891.6) | ($35,664) | $8,561 | ($27,103) |
Total Savings | *890 Man Hours | 89% Labour Savings | Material Costs are higher |
65% Overall savings for shipyard |
Benefits of Pyplok® weldless fittings versus welded fittings:
- No special skilled labour required vs. qualified welder
- Actual swaging time in seconds vs. hours for a welded joint
- No special hot work permits
- No fire watch personnel required
- No leaks as a result of stress fatigue cracks as seen in welds
- No off loading or purging of fluids and gases
- No cost to x-ray welds
- No cost to rework welds
- No acid flush chemicals and neutralizers required
- No added cost or environmental issues to dispose of chemical waste
- Safe and easy to install in tight confined places
- Safe permanent, tamper-proof connection
- Safe cold work fitting technology