Prefabricated Piping Systems
Unlike with field-fabricated pipe systems, pipe prefabrication calls for front-end engineering. Customers provide all available detailed information, including equipment location, plan, elevation drawings, and 3D Model. We use this data along with direct customer feedback to establish the proposed pipe route for the system.
For complex systems, Tube-Mac® uses 3D scanning services to provide dimensional information of each customer’s equipment and surroundings. Our advanced hardware and software ensure precise and reliable data capture and analysis for the customer’s unique industrial applications.
3D scanning is essential for replicating the existing components, walls, and trenches through which the piping may run, especially when original design data is unavailable. Our 3D scanning services achieve this with exceptional accuracy and efficiency. Tube-Mac® can create detailed and accurate digital models to seamlessly integrate into industry-standard CAD software such as Autodesk Inventor.
Tube-Mac® has all the pipe fabrication equipment required in house with fully trained technicians.
Benefits of prefabrication
- Time and cost savings
- Quick reassembling in the field
- Simplified onsite installation
- No special skilled labour (i.e. qualified welder) required
- Excellent quality and cleanliness in a workshop-controlled environment
- Pre-washed cleaned and capped pipes maintain cleanliness during shipping
- Reduced onsite oil flushing time
Prefabrication Services
- Bending
- Pipe end forming
- Flaring, 37° and 10°
- Retain ring grooving
- Wall forming
- Powder coating or general paint specs
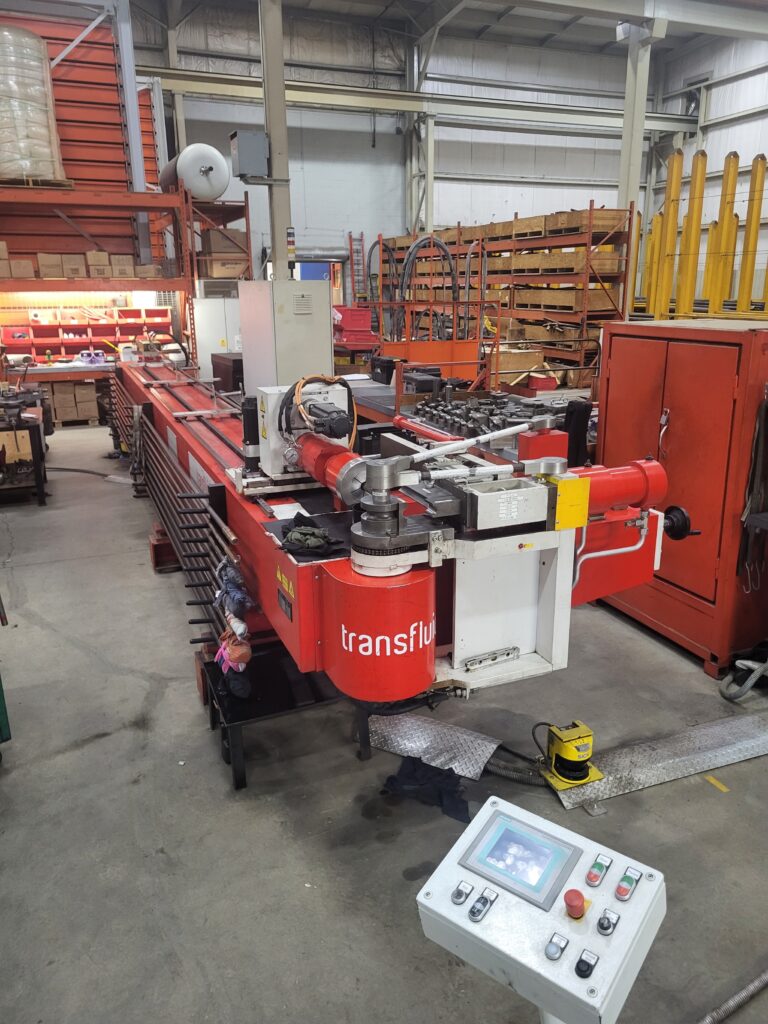
Prefabrication Process
- Prefabrication begins with the accurate pipe design and layout.
- Pipes are properly measured and cut to the required length. The pipes are then bent with cold bending machines. Non-standard, large diameter pipes and special radii requirements are bent using induction bending.
- After bending, the pipe ends are prepared for flaring or retain ring grooving.
- Internal cleaning and capping of each pipe is performed to maintain cleanliness during shipping.
- External protection is applied by powder coating or painting in accordance with the customer’s requirements.
- Proper export packing and protection ensure the quality of the delivered piping spools.
- The use of prefabricated pipe spools ensures the highest possible quality as well as an easy and fast installation. In some cases, to further speed up the installation smaller pipe sizes up to 2” (60mm) can be assembled in groups directly onto support brackets and clamp assemblies.
Why Choose Tube-Mac?
When you bring Tube-Mac® into your project, you can expect the following benefits:
- Cost Savings
- Extensive Inventory
- Turnkey Solutions
- Global Network